2022 High quality Tube Bending - Custom CNC pipe tube bending service – LAMBERT
2022 High quality Tube Bending - Custom CNC pipe tube bending service – LAMBERT Detail:
Short Description
Pipe bending is a process in which a pipe is first loaded into a bender or pipe bender and then sandwiched between two dies (clamping block and forming die). The tube is also held loosely by two other molds, the wipe mold and the pressure mold.
The tube bending process involves using mechanical forces to push the material tube or tubing against the mold, forcing the tubing or tubing to conform to the shape of the mold. Usually, the feed tube is held firmly in place as the ends rotate and roll around the die. Other forms of processing include pushing a blank by rollers that bend it into a simple curve. [2] For some pipe bending processes, a mandrel is placed inside the pipe to prevent collapse. The tube is held in tension by a scraper to prevent any creases during the pressure process. Wiper molds are usually made of a softer alloy, such as aluminum or brass, to avoid scratching or damaging the bent material.
Most tools are made of hardened or tool steel to maintain and extend tool life. However, softer materials, such as aluminum or bronze, can be used when there is concern about scratching or gouging the workpiece. For example, clamping blocks, rotary forms, and pressure dies are usually made of hardened steel because the pipe will not move through these parts of the machine. Press and wipe dies are made of aluminum or bronze to preserve the shape and surface of the workpiece as it slides.
Pipe benders are usually human-powered, pneumatic, hydraulically assisted, hydraulically driven or electrically driven servo motors.
Product Description
Bending
Bending was probably the first bending process used on cold pipes and tubing. [Clarification needed] In this process, a curved mold is pressed against the pipe, forcing the pipe to fit the shape of the bend. Because there is no support inside the pipe, the shape of the pipe will deform somewhat, resulting in an oval cross section. This procedure is used where a consistent pipe cross section is not required. Although a single die can produce a variety of shapes, it only works for tubes of one size and radius.
Rotary stretch bending
Complete set of tools for rotary stretching and bending
Rotary tension bending (RDB) is a precision technique because it is bent using a tool or “die set” with a constant centerline radius (CLR), or expressed as the average bending radius (Rm). The rotary stretch bender can be programmed to store multiple bending jobs with varying degrees of bending. A positioning index table (IDX) is usually attached to a bending machine, allowing the operator to reproduce complex bends that may have multiple bends and different planes.
Rotary stretch bending machines are the most popular machines for bending tubing, pipes and solids for the following applications: handrails, frames, motor vehicle roll racks, handles, wires, etc. When the right tool is matched to the application, the rotary stretch bend produces a beautiful bend. CNC rotary stretch bending machines can be very complex and use complex tools to produce severe bending with high quality requirements.
The complete set of tooling is required only for high-precision bending of hard-bending tubes with large OD/ T (diameter/thickness) and small average bending radius Rm and OD. [3] Axial pressurization on the free end of the pipe or on the die helps prevent excessive thinning and collapse of the outer convex part of the pipe. Mandrel, with or without ball, with spherical link, mainly used to prevent wrinkling and ellipticity. For relatively easy bending processes (i.e., with a reduction in the coefficient of difficulty BF), the tool can be gradually simplified to eliminate the need for axial AIDS, mandrels, and finishing edge dies (mainly used to prevent wrinkling). In addition, in some specific cases, standard tools must be modified to meet the specific requirements of the product.
Roll bending
Main entry: roll bend
During rolling bending, the pipe, extruded piece, or solid applies pressure to the pipe through a series of rollers (usually three), gradually changing the bending radius of the pipe. Pyramid rollers have a moving roller, usually a top roller. A double pinch roll bender has two adjustable rollers, usually a bottom roller and a fixed top roller. This bending method results in minimal deformation of the pipeline cross section. The process is suitable for producing spiral pipes and long bends such as those used in truss systems.
Three-roll bending
Three roll push bending process
Three-roll push bending (TRPB) is the most common free bending process used to create curved geometries consisting of multiple planar bending curves. However, 3D plastic surgery is possible. The profile is guided between the bending roller and the support roller while being pushed through the tool. The position of the forming roller defines the bending radius.
The bend point is the tangent point between the pipe and the bend roll. To change the bending plane, the thruster rotates the tube around its longitudinal axis. Typically, TRPB kits can be used with traditional rotary stretch-bending machines. The process is very flexible because multiple bending radius values Rm can be obtained using a unique tool set, although the geometric accuracy of the process cannot be compared with rotary stretch bending. Curved profiles defined as spline or polynomial functions can be produced.
Simple three roll bending
Three-roll bending of tubing and open profiles can also be done using simpler machines, usually semi-automatic and non-CNC controlled, capable of feeding tubing into the bending area by friction. These machines usually have a vertical layout, with three rollers on a vertical plane.
Induction bending
Induction coils are placed around a small section of the tube at the bend point. It is then sensitively heated to 800 to 2,200 degrees Fahrenheit (430 to 1,200 degrees Celsius). When the pipe is very hot, pressure is applied to bend the pipe. The pipe can then be hardened with air or water spray, or the ambient air can be cooled.
Induction bending is used to produce bends suitable for a wide range of applications, such as (thin-walled) pipes for upstream and downstream as well as onshore and offshore parts in the petrochemical industry, large radius structural parts in the construction industry, thick wall, short radius bends for power generation and urban heating systems.
The main advantages of induction bending are:
You don’t need a mandrel
Bending radius and Angle (1°-180°) are optional
High precision bending radius and Angle
It is easy to produce accurate tubes
Significant savings can be achieved in field welding
One machine can accommodate a variety of pipe sizes (1 “OD to 80″ OD)
Excellent wall thinning and ovality values
Product detail pictures:
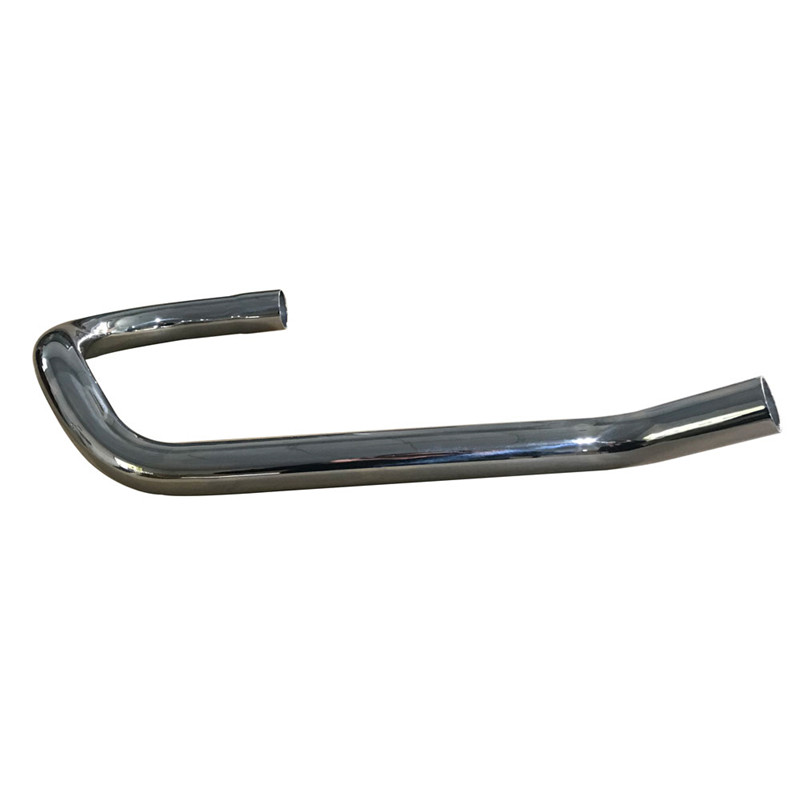
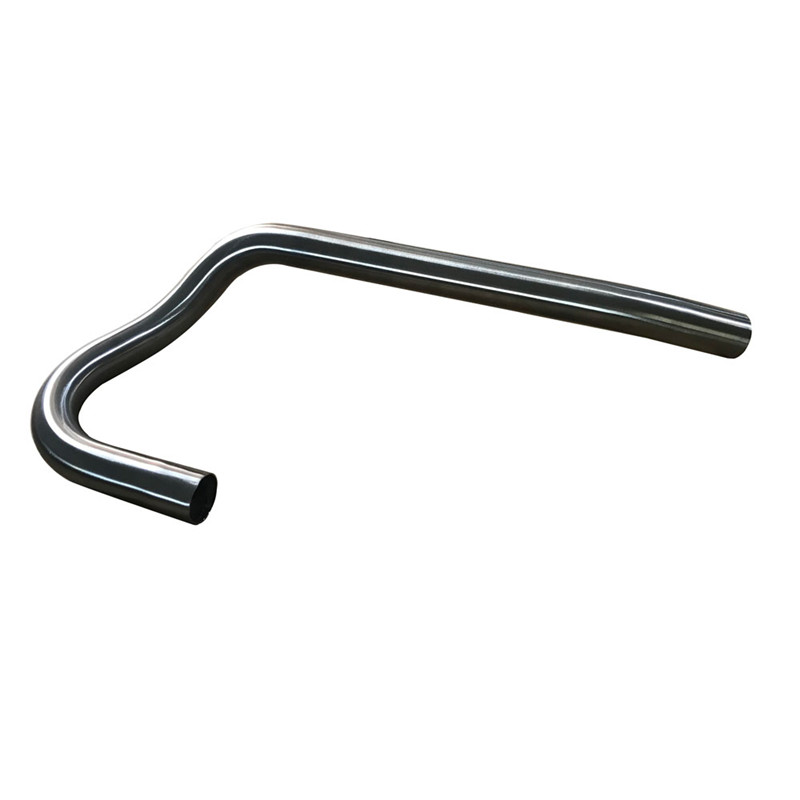
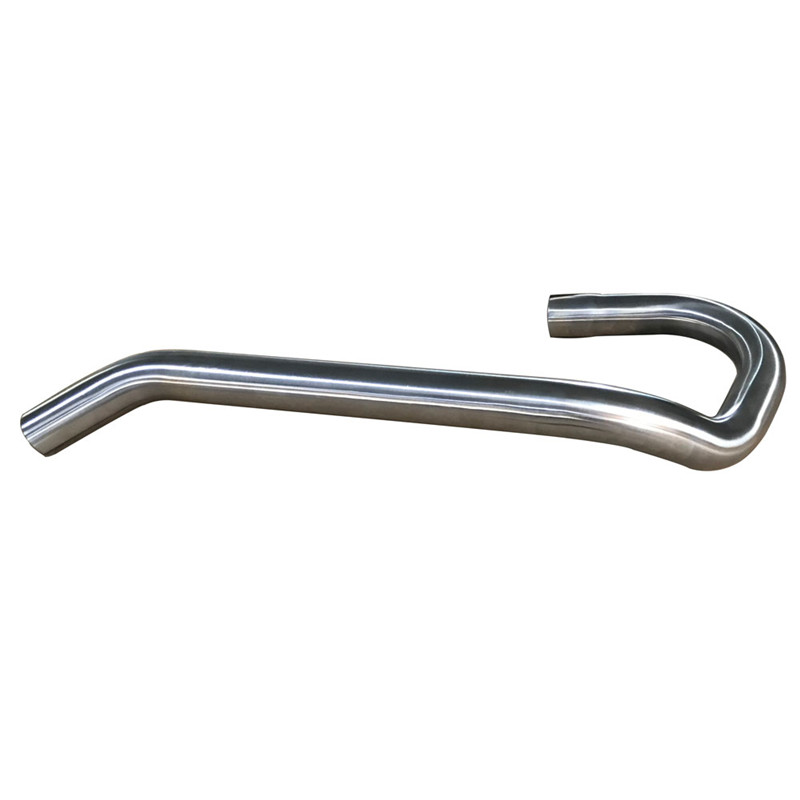
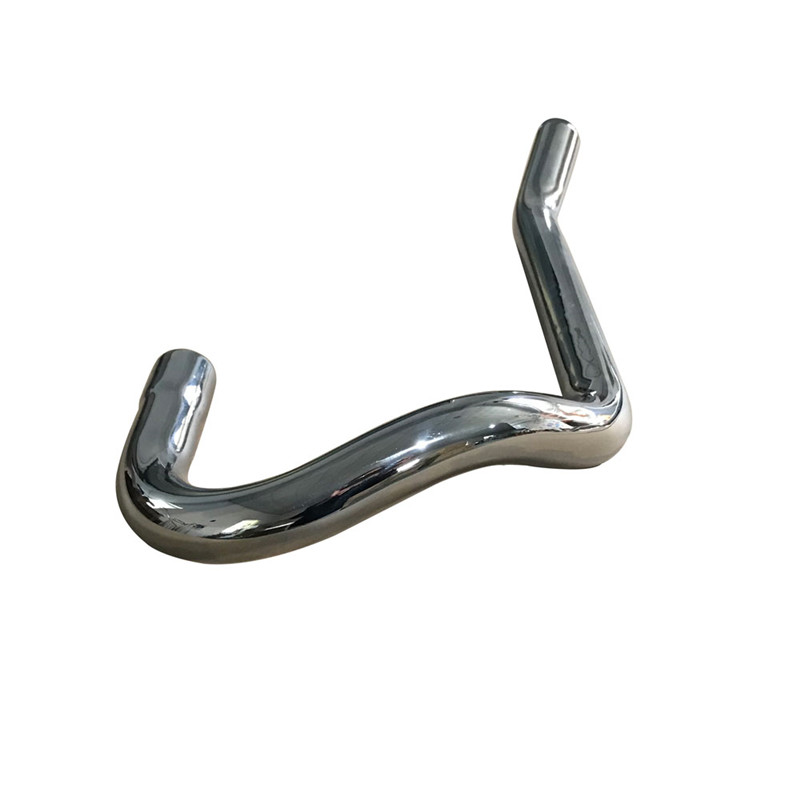
Related Product Guide:
We've numerous great employees customers excellent at promoting, QC, and working with kinds of troublesome difficulty inside the generation method for 2022 High quality Tube Bending - Custom CNC pipe tube bending service – LAMBERT , The product will supply to all over the world, such as: Kuwait, Malaysia, Angola, Profession, Devoting are always fundamental to our mission. We have always been in line with serving customers, creating value management objectives and adhering to the sincerity, dedication, persistent management idea.
Lambert sheet metal custom processing solutions provider.
With ten years of experience in foreign trade, we specialise in high precision sheet metal processing parts, laser cutting, sheet metal bending, metal brackets, sheet metal chassis shells, chassis power supply housings, etc. We are proficient in various surface treatments, brushing, polishing, sandblasting, spraying, plating, which can be applied to commercial designs, ports, bridges, infrastructure, buildings, hotels, various piping systems, etc. We have advanced processing equipment and a professional technical team of over 60 people to provide high quality and efficient processing services to our customers. We are able to produce sheet metal components of various shapes to meet our customers’ complete machining needs. We are constantly innovating and optimising our processes to ensure quality and delivery, and we are always “customer focused” to provide our customers with quality service and help them achieve success. We look forward to building long-term relationships with our customers in all areas!

Cooperate with you every time is very successful, very happy. Hope that we can have more cooperation!
