What is Sheet Metal Fabrication?
Sheet metal fabrication refers to the turning of flat metal sheets into metal products and structures. Typically, this technique involves transforming different types of sheet metals into parts and components. It is also a versatile process that can create a wide range of metal components made from Aluminum, Steel, Stainless Steel, Copper, and Brass.

In sheet metal fabrication, different techniques are usually combined to produce the desired part. The basic processes include cutting, bending, punching, stamping, welding, and finishing. These techniques complement each other and play a vital role in the successful completion of a project.
What’s more, you are unlikely to go about your day without encountering sheet metal products. So, whether you’re at home, at work, or out and about, it’s highly likely that you find these products everywhere. This is a testament to the durability, versatility, and ubiquity of metal manufacturing.
The Process to Create Sheet Metal Parts
Sheet metal fabrication can be complex and challenging to understand for many people, leading to unrealistic expectations and requirements for a project. It is important to note that the process of creating metal parts involves several steps from start to finish.
The Idea
Every rapid prototyping process begins with an idea, and sheet metal design is no exception. It begins with basic concepts of what you want as a designer. You can put these ideas down roughly to provide realistic requirements for your project. It may also involve the designing of a 3D model of the desired component. The model often includes requirements for wall thickness, bend radii, hole orientation, bend allowance, and more.
Creating Engineering Drawings
After the completion of a 3D model, there is a need to create drawings for manufacturing. Before any work can begin, engineers need to develop blueprints. These blueprints will determine the specifications of the sheet metal needed to make initial drawings.
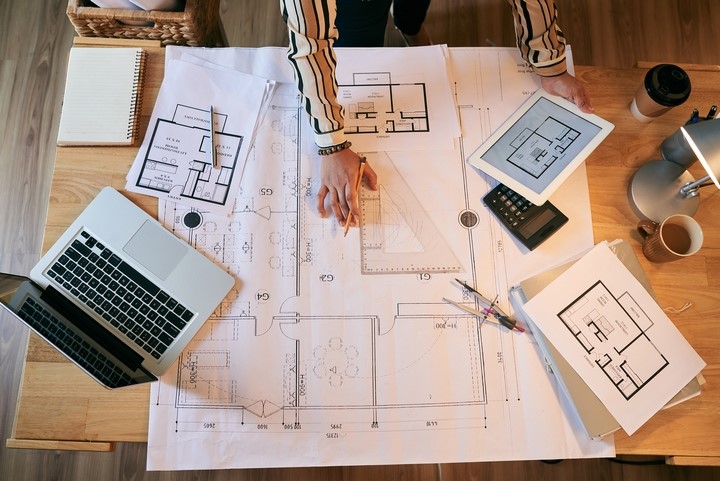
The drawings are what will be sent to the machine shop. The drawings often include all manufacturing information such as material selection, surface finishing, and more.
Manufacturability Analysis
Along with other related calculations, the drawings will be rechecked to ensure they follow requirements and specifications. Following a DfM strategy helps to focus on simplifying the designs and possible reduction of part counts. Such analysis suggests standardizing parts for various applications.
Furthermore, engineers will get insights into developing designs that can be easily manufactured. Once the manufacturability analysis is complete, there will be a final shop drawing with in-depth calculations of stress/strain levels and load limitations. The information available therein will determine the sheet metal fabrication process.
Prototype Development
Once there is a sheet metal design model, engineers carry out several processes to maintain the component’s geometry. These methods include cutting, bending, punching, stamping, and welding. For projects requiring rapid prototyping, these processes are crucial to ensuring that the prototype maintains both precision and functionality. Surface finishes also help to improve the aesthetics of the created prototype. It is important to carry out these steps one after the other. Rushing through the process or skipping one step may compromise the quality and integrity of the final product.
Prototype Testing
After developing the prototype, clients then evaluate the prototype to ensure that it meets their requirements. The testing may also involve using such components in real-life conditions. Also, evaluation can be done with users giving feedback on the products.
Full-Scale Production
A prototype that passes testing and meets the required specification will go into full part production.
Post time: Nov-04-2024